Basics of Designing an Underground Infiltration Basin
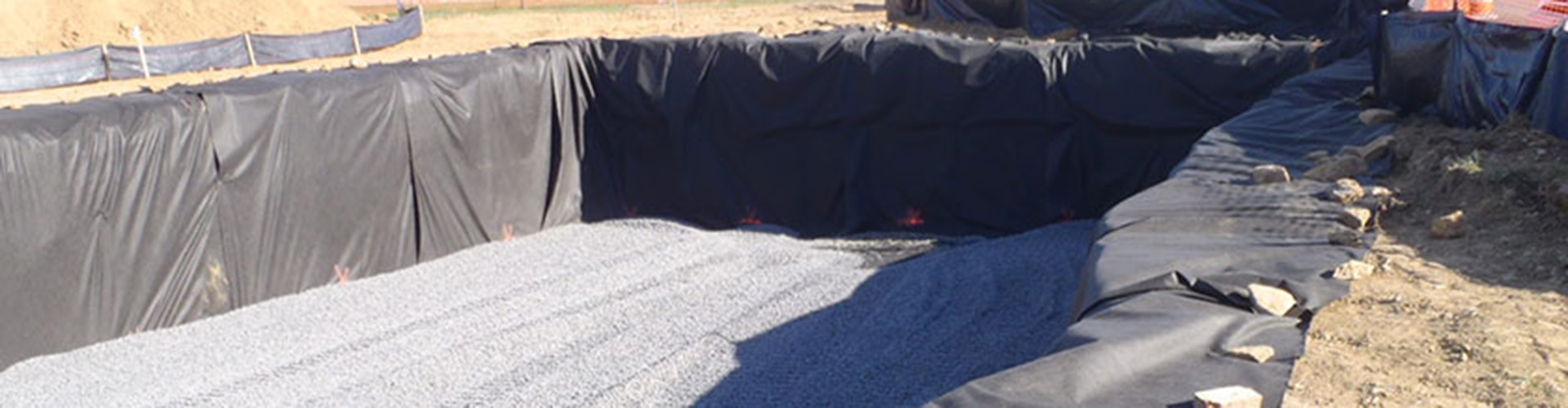
The design of every underground stormwater system is unique, so it’s important to develop a site-specific plan. However, the first step in this process should always be the same: completing a soil evaluation. This will determine the properties of the soil, any limiting zone depths, and the applicable infiltration rate.
Infiltration Rate
As part of the soil evaluation, an infiltration test will be performed at the infiltration interface elevation. For an underground infiltration basin, this elevation is the stone/soil interface at the invert of the system.
The most common test is a double-ring infiltrometer test where a double cylinder is embedded into the native soil and both the inner and outer cylinders are filled with water. As the water is allowed to percolate into the native soil, the results of the drop in the inner cylinder are measured. This data is recorded in conjunction with the length of the test, providing a rate in inches per hour.
Subgrade Design
Subgrade design is a vital part of the long‐term performance of the infiltration basin. This includes not only the infiltration capacity of the system but the structural stability. The soils that support the structure must be adequate in bearing capacity to support the weight of the system, backfill materials, and any live loads applied at the surface. In addition, the soils must maintain adequate resistance to differential settling. Therefore, the results of the soil evaluation will need to be utilized to determine if the soils are capable of providing adequate support or if further mitigating measures, such as soil compaction, are required.
Treatment Capacity
The required treatment capacity of the infiltration basin will be dependent upon local regulations. This could vary from the first inch of rainfall on the drainage area to evaluations that are more detailed. Once the volume is determined, the engineer will need to ensure that an adequate installation footprint is provided for both capacity and loading ratio.
The volume that needs to be infiltrated, the infiltration rate, and the allowable infiltration time (24‐48 hours) will determine the square footage of the installation.
Separation Fabric
A common concern surrounding underground infiltration trench design is specifying a separation fabric to be used at the stone/soil interface and the stone/product interface. Both areas require separation but for different reasons. The stone/soil interface utilizes the fabric to prevent the soils and stone from migrating as the soils become saturated. And the stone/product interface needs the fabric to prevent the backfill material from entering the product through the void space in the side panels and platens.
Based on these needs and the application standards, engineers have a choice to make between woven and non-woven geotextile fabric. Non‐woven geotextile fabric is the primary method, but for some sites, there is concern that the small, open areas between fibers will become clogged with sediment. If this is a concern, engineers can specify a woven alternative that will not allow particles to be captured in the fabric.
Pretreatment and Maintenance
The long-term performance of an underground infiltration basin is dependent upon preventing sediment from entering the system. By installing a pretreatment system, sediment will not have the opportunity to clog the fabric, fill the leveling bed, or clog the micropores of the soil.
The inclusion of a pretreatment device will also limit the frequency with which a system needs to be maintained but it will not remove the requirement. Proper system maintenance is necessary to remove any sediment buildup and ensure that the infiltration basin is operating as designed. If maintenance is not completed, systems run the risk of reduced storage capacity and infiltration rate. A tip for making maintenance easy is to provide areas for sediment capture and removal as part of the system design, eliminating the need to trace the entire system.